Pre Fabricated Building
Pre Fab Building
Prefabricated light constructions are mounted on the ready-prepared concrete floor. The greatest advantage of prefabricated buildings is being earthquake-resistant and light as they are steel constructions.
The short manufacturing period, providing fast mounting and having the feature to dismount and mount over and over again increase the reasons of preference for these prefabricated structures.
Prefabricated buildings are produced in required size and design. The structures can be one storey as they can be produced in two or three storeys. Product shipments are made with trucks, semi-trailer trucks, ships, freight containers, trains or cargo planes. There is no requirement for cranes in the loading and unloading of fibercement plated panel system structures. Crane is required for fibercement bolted type building and steel sheet panel system buildings.
The prefabricated buildings can be delivered with electrical and sanitary installation, paint and window glasses included as they can be delivered without them. The fibercement plate we use as siding material in exterior, interior, roof and mezzanine floor sidings consists of OPT brand of cement, silicate and cellulose fiber and ovendry produced in high pressure and heat. The deformation of the plate from temperature variance and climate conditions is prevented with this process.
Optpeb Modular Building
What is foam concrete and how it is made?
Foam Concrete is also Known as Cellular light weight concrete, "CLC‟, Foamed cement, Light Weight Concrete across the world with its greater advantages from 5 years. The basic foam concrete is made from mixing aqueous foam which is produced from generators into Slurry of Cement, fly ash or sand, water and other additives in a precise mixing in foam concrete mixer for accurate mixing without disturbing its original chemical and physical properties. The Final mixture Results many small air cells uniformly distributed throughout the concrete which will creates cellular structural material densities ranging from 300kgs/m³ to 1800kgs/m³ with compressive strengths between 5kgs/cm² to 200kgs/cm². The Precise Controls of the volume of air cells in foam concrete will results controlled densities and strength's of foam Concrete. The final mixture is either pumped or transfers manually for casting of blocks, panels, precast items, prefabricated houses, void fillings, roof insulations, floor Screeds and many other applications without any vibration or Compaction. Foam Concrete manufacturing consumes higher amounts of fly ash (which is waste material from thermal power stations) hence it is consider as green building material. At present foam concrete is using in construction for many applications throughout the world from last four to five decades.
If we compare the modern methods and conventional method of wall construction there is lot of scope and advantages of modern material and method in the construction of infill wall, than that of conventional material and method, as they not only are green building material but they can also lead to lot saving in time and cost if it incorporated in the design part of the project.
STEP 1- FOUNDATIONS
Foundation for the uilding is made In accordance with type of building and load its capacity.
STEP 2- STEEL STRUCTURE
Steel structure is mounted on the prepared foundations.
STEP 3- SERVICES
Arrangement of the Service Lines: Electrical & Water Lines/ Sewage Pipe. Fixing of the Ventilation system
STEP 4- SHUTTERING
Heavy combined panels serves as temporary cast formwork inside and outside of the wall. The panels are fixed to the steel frame using screws.
STEP 5- CASTING
Light Weight Foam Concrete prepared in Special Machines is then poured between the installed panels, completely filling the space.
Why Steel ?
Steel is Economic:
Steel is Economic:
Prefabricated load bearing elements provide high quality for reasonable prices and shorten the construction period to a great extend. Steel is the material that has the highest ratio of load bearing capacity / weight. Thanks to its high load bearing capacity steel structural members are produced as small profiles and sizes, lighter and at perfect quality. As the sizes of the load bearing elements are far smaller than wood and concrete, usable space is a lot bigger in steel buildings, which enables a more efficient use of the building’s space. Price balance and short construction periods offer early moving in options with cost advantages i.e. paying fewer rents or less interest rate.
Steel is Earthquake Resistant:
Steel is the most resistant construction material thanks to its high resistance, flexibility and lightness. As it is a very light material, it can resist to impacts without breaking apart. The only factor to reduce the earthquake force is to lighten the building. Because the bigger the mass of the building is, the stronger the force of the earthquake to be imposed on the building is. Steel houses are 5 times lighter than the concrete buildings. This means that the earthquake force to be imposed on the building is 5 times smaller.
Steel is Environmentally Friendly:
Steel is a durable and reusable material. Materials obtained from the removal of steel buildings are recycled. A building’s skeleton made of light-gauge steel can be recycled from 7-8 old cars. On the other hand 50 trees need to be cut to build a similar house of wood.
Steel is Quick:
Building up process is very quick and independent from weather conditions in steel construction as concrete is not needed except for the foundation and subbasement. This allows a decrease in the need for capital and in the construction costs. Assembling of a 200 m2 house can be completed in only 7 days.
Steel is of High Quality:
Quality of steel which is a completely industrial product that is produced all over the world at the set standards is checked and certified in every production step. Manufacturers or users cannot intervene with its physical features. Theoretical calculations are valid at the implementation. As it is not hidden in concrete it can always be checked against the project and standards.
Galvanized Steel doesnt Corrode:
Galvanized steel is used in the light-gauge steel frame manufacturing so the resistance against corrosion is high, it doesn’t rust.
Steel is Flexible:
Adaptation to our rapidly changing life styles can be more easily and economically provided in steel buildings. Partition walls can be removed or their places can be changed to meet your changing needs even years after the construction.
Steel doesnt pose danger in terms of Lightening:
Unlike other frame systems steel construction doesn’t pose danger in terms of lightning, because the protection installation creates a path going towards the land and diminishes the risks of explosions, small sized fires and injuries.
Light Gauge Steel Building Technology
In this building type structural members are manufactured by cold forming the galvanized steel. Structural elements that are manufactured under control and supervision by modern machines are brought to the construction site and assembled. For this reason human errors are minimized in light-gauge steel buildings. Additionally, as on site manufacturing is reduced to minimum, errors and damages commonly seen at the construction site are dealt with. Even because of only these characteristics light-gauge steel building systems are far better than conventional reinforced concrete buildings.
Buildings constructed with Light-gauge Steel Building System weight less than the reinforced buildings in the same size, therefore the load affecting the building in the earthquake is less which increases the system’s earthquake resistance. Because the load bearing capacity / weight ratio of the light-gauge steel systems is quite high.
Also plastic deformation behaviors of these buildings are more efficient than reinforced concrete buildings; therefore no sudden collapses occur in an earthquake which enables the building to remain standing safely after the earthquake.
Construction phases of steel buildings resemble the phases of conventional reinforced concrete buildings. The building is designed, architectural and static projects are prepared. Then the steel frame construction starts. The production takes place in the factory flawlessly. Floor, wall, roof, etc components of the building are manufactured as galvanized steel profiles in appropriate sizes. These profiles are sent to the construction site without loss, either as profiles or as panelized parts, considering the distance of the construction site and the transportation conditions. Profiles are assembled by expert assembling teams at the construction site in line with the architectural plan. Only special studs are used during the assembly, no welding is done. When the assembly is done, the frame is filled with insulation materials (fiberglass, rock wool, etc.). Walls are covered with OSB (Oriented Standard Board) or similar materials.
Taking the speed of construction and credit facility potential into consideration, Light-gauge Steel Building System is very advantageous in terms of costs. The primary factor increasing the costs in a construction project is the time. Reinforced concrete buildings take longer time to be completed. As light-gauge steel buildings can be completed in a very short period of time and errors caused by craftsmanship are minimized, they are more cost efficient in terms of money and time.
It is possible to manufacture any type of design with the Light-gauge Steel Building System. Either modern or traditional, all dwellings can be constructed elegantly with this system. Local features and preferences can easily be reflected on these buildings. Dwellings can be designed as detached, semi-detached or terraced houses. Light-gauge Steel Building System can also be very successfully implemented on other building types. Social buildings such as schools, hospitals, dormitories, nurseries, malls and marketplaces are commonly constructed public projects. As life safety is the basis of the Light-gauge Steel Building System, typical ceiling height is 3.00 m. However it is possible to make it longer by using conventional rolled steel components. 4 storey buildings constructed with Light-gauge Steel Building System are important as they meet the needs of our people in addition to being safe in terms of earthquakes. More and more beautiful and classy garden villas constructed with a fast and economic technology are offered to public.
The construction speed of a building may vary depending on the size, shape, whether it has a basement floor or not, location, and that region’s climate and topography. These parameters, without doubt, are also valid for low-rise reinforced concrete buildings.
However, when Light-gauge Steel Buildings System is compared to reinforced concrete system, it is obvious that steel building system is built quicker and even without causing any environment and noise pollution as they come out of the factory faultlessly.
Earthquake Resistance of Steel Buildings
Earthquakes are one of the most destructive forces in nature. In recorded history, single seismic events have altered the course of major rivers, erased land masses from the map, and devastated man-made structures within a considerable distance of the earthquake epicenter. Frequently, earthquakes also produce additional hazards such as tidal waves (tsunami) and fire caused by damage to the infrastructure of a populated area. The inevitable consequence of any major seismic event is the loss of life. Improvements to design and construction methods in the United States over the past 50 years have helped make the modern home a safer habitat during an earthquake. One of them, the use of light gauge steel framing, offers very real advantages over traditional concrete and wood framing should an earthquake strike.
What Happens to a House During an Earthquake?
The earthquake (seismic) forces that can destroy a house are produced by strong and erratic side-to-side and up-and-down movements in the ground (see Earthquake movements). Structural damage is typically caused by "inertia", or the reluctance of the upper portions of a structure to begin moving once the ground has shifted, and then conversely, to stop moving once the structure has begun moving. When the earth shifts sideways, the effect of inertia on a house is similar to that experienced by players in the game "crack the whip." If the movement is vertical, inertia causes the structure to be compressed as the earth rises and "telescoped" as the ground stops moving. Homes are designed to resist the stresses of inertia by absorbing the energy that is produced by earthquakes. This is commonly accomplished by allowing the structure to "flex" with the ground movement in varying degrees, depending upon the material used to build the house, design of the structure, quality of construction, level of engineering, and the applicable building code.
Engineering a House for Earthquakes:
Houses framed with either wood or steel rely on the same basic design concept. Induced lateral forces, such as those produced during an earthquake, subject the structure to sliding and "racking" (see Racking Motions in a two-story residential structure). To control this motion, the roof and floors must be tied to the walls all the way down to the foundation. In addition, "racking" must be limited to tolerable levels. The roof and floor between stiff walls (those designed to limit racking) must be designed to limit motion and transfer loads to the walls and, ultimately, the foundation.
Since the lateral forces are primarily generated at the floor and roof levels, walls will tend to "uplift" and "overturn". This is controlled by tying the walls together to reduce uplift forces and ultimately fastening the walls to the foundation.
Earthquake Resistance of Steel Buildings
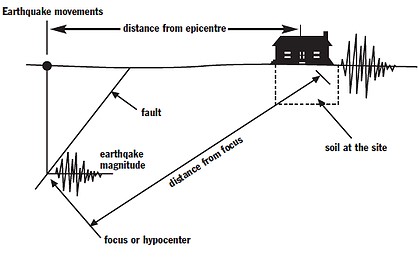
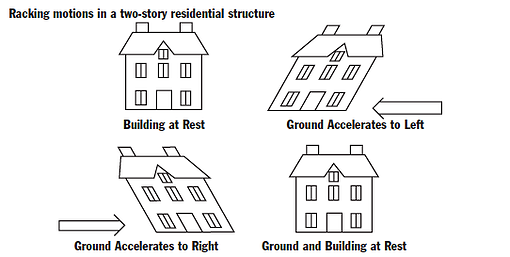
Light Gauge Steel Construction:
Most regard light gauge steel framing as a modern concept, although it has been used in both residential and commercial construction for many decades. So, while steel framing has recently become a viable contender in the home building industry, it has a reliable track record over an extended period for consistent performance as a structural material. There is no difference between the appearance of a home framed with light gauge steel and one framed with wood. Rather, the most significant difference between a steel framed house and another framed with wood is determined by how well the framing material can provide long-term, consistent performance; for example, sagging roof lines typically found in an older wood framed home are not evidenced in steel framed homes.
Advantages of Light Gauge Steel in an Earthquake:
Earthquakes are unpredictable in terms of magnitude, frequency, duration, and location. Consequently, the ideal structure to withstand earthquake forces will behave in a consistent and predictable manner. Unlike wood, light gauge steel is capable of meeting this standard due to the strict process used to manufacture steel studs, the inherent properties of steel, andtypical construction methods used in steel framing. Specific advantages offered by the use of steel framing in a seismic event include the following considerations:
SUMMARY
The purchase of a home is the single largest investment that most people will ever make. As a result, structural and nonstructural problems during the life of a house can be both financially and emotionally draining. In California, where earthquakes are more frequent and violent than anywhere else in the United States, the prudent homeowner will take necessary precautions to protect against loss. Building with steel should be considered at the top of the list.
How many floors can we make ?
Loom Crafts has developed a unique, standardized, cold formed steel (CFS) structural system capable of going to Ground + 4 stories.
The Loom Crafts structural system is automatically integrated into building plans during the architectural design process via various designing softwares. A fully engineered and detailed structural plan and virtual model is complete very early in the design process, automatically.
Loom Crafts structural system is panelized and manufactured to very tight tolerances. It is assembled in a fraction of the time of other structural approaches. We use best quality steel and significantly reduce waste by employing an off-site panelization process.
We install our structure using a lean manufacturing approach – we do it faster, and with greater quality control than other structural assemblies. We reduce site impact and site waste significantly.
Difference between Conventional & Steel Construction
Prefab homes can be confusing at first because there are many different names for them. They are labeled prefabricated, modular, prefabricated, and even incorrectly called manufactured. Putting names aside, what is a Prefab home? Is it different from a traditionally built home? Yes. There are quite a few differences between these two types of homes that are important for every prospective homeowner to know.
Their planning stages are often different. With traditional homes a prospective homeowner may need to draft plans with an independent architect or possibly pick a style from a book. Prefab homes are usually planned with the company that will build the home. Some companies, such as Loom Crafts, will work with customers during every step of the planning process to create plans that fit the customer’s style while remaining functional.
When the building process begins the two types of homes split even more. Prefab homes are built inside a factory while traditional homes are built at the construction site. Factories will often use an assembly line style process to build a home, but Loom Crafts Homes approaches the building process differently. We give each home a designated space where it is built instead of passing it along a line. This process is more efficient than an assembly line, so construction time is reduced.
It usually takes eight to ten weeks to build a Prefab home once the planning process is completed. A traditional home can take several months to complete due to unforeseen delays. Prefab homes do not have this problem because the environment they are built in is controlled. The temperature is controlled to keep the quality materials in their original state. Building inside also protects the construction area from the elements, so there are no delays due to weather. Traditional homes are at the mercy of the environment and subject to quite a few delays. These delays may range from weather to waiting for materials. Having a shorter building process also means a Prefab home will be less expensive, because a customer will use less of their construction loan.
Once a Prefab home is completed it is then transported in pieces to the construction site. At the site the home will be put together on the foundation. With Loom Crafts Homes the foundation will already be laid, so the assembly can start immediately. Also, Loom Crafts does all the assembly on site, instead of simply dropping it off, to ensure consistency and quality workmanship.
Building a Prefab home is convenient for the customer because they have less to worry about. Construction sites get messy with garbage. With a Prefab home all the garbage is taken care of at the factory. Traditional homes sometimes require prospective homeowners to deal with extra services, such as a dumpster service.
Prefab homes are often built to be smaller than a traditional home, but this does not happen all the time. Loom Crafts builds homes in a range of sizes to meet the needs of each customer. We build smaller structures, including a home that was 300 square feet, and we also build large structures.
There are other differences between Prefab homes and traditional homes, but they are much smaller. These two types of homes are built very differently and each method will produce a functional home. However, Prefab homes do tend to have more benefits than negative qualities. They are different from the traditional home building process, but their difference is a homeowner’s gain.